Mascara-Bürsten – mit hohem Tempo zum Prototyp
Die Entwicklung eines Prototyps für eine Mascara-Bürste dauert in der Regel bis zu 18 Wochen. Dank eines neuen Kunststoffpulvers ist es der Division Applicator Systems nun gelungen, den Prozess markant zu beschleunigen und einen Prototyp innerhalb einer Woche anzufertigen.
Zeit ist Geld – das gilt auch für die Kosmetikbranche. Bis eine neue Wimperntusche in die Verkaufsregale kommt, ist es ein langer Entwicklungsprozess. Denn trotz ihrer vermeintlichen Ähnlichkeit bestehen erhebliche Unterschiede zwischen den verschiedenen Mascaras. Wimpern sind Teil des persönlichen Ausdrucks und werden in unterschiedlichen Kulturen unterschiedlich betont. Deshalb ist es wichtig, dass eine neue Wimperntusche unter realen Bedingungen getestet wird.
Zu steif für Tests
Bisher wurden Prototypen für Mascara-Bürsten mithilfe von 3D-CAD-Programmen (CAD = computer-aided Design) und einem harten Kunststoffmaterial gefertigt. Der Entwicklungsprozess dauerte bis zu 18 Wochen, da der Hersteller zunächst eine Zeichnung anfertigen und anschliessend einen visuellen Prototyp im 3D-Druckverfahren anfertigen musste. Die Zeichnungen galt es gemäss den kundenspezifischen Bedürfnissen nochmals anzupassen, bevor ein Pilotwerkzeug für den Spritzguss hergestellt werden konnte. Für jede einzelne Borste musste dabei ein kleiner Hohlraum, eine sogenannte Kavität, in das Spritzgusswerkzeug hineingefräst werden. Erst nach Anfertigung des Prototyps hatte der Kunde die Möglichkeit, die Bürsten visuell zu beurteilen. Die Borsten dieser Prototypen waren aber zu steif, um sie im praktischen Einsatz zu testen. Hinzu kommt, dass der Produktionsprozess zeit- und kostenintensiv war.
„Kurz gesagt: Wir wollen profitabel wachsen“
Sulzer baut das Geschäft mit Applikatoren aus. Amaury de Menthiere, Leiter der neuen Division Applicator Systems (APS), erklärt, wie Mascara und Ähnliches zum Geschäftsmodell von Sulzer passen und welche Ziele er für seine Division anpeilt.
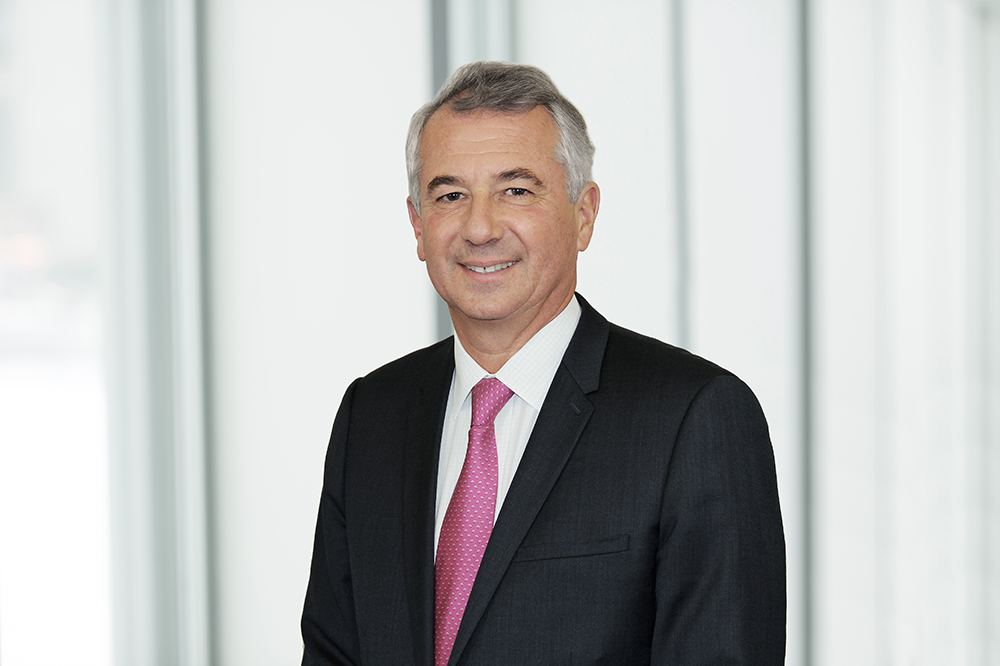
Amaury de Menthiere, Divisionsleiter Applicator Systems
Sulzers Übernahme von Geka überraschte viele Marktbeobachter. Wie sollen Mascara, Lipgloss und andere Kosmetikartikel zu einem Schweizer Industrieunternehmen passen?
Amaury de Menthiere: Die meisten kennen Sulzer als Hersteller von Pumpen für die Märkte Öl und Gas, Energie und Wasser. Doch Sulzer ist viel mehr als das. Über sein Mixpac-Geschäft liefert das Unternehmen seit vielen Jahren Applikatoren für die Bereiche Bau und Klebstoffe sowie für die Dental- und Gesundheitsbranche.
Wie passt Geka dazu? Schauen Sie sich in den Werkhallen um – Mixpac und Geka arbeiten fast mit denselben Produktionsmaschinen. Beide Unternehmen stellen ihre Produkte im Spritzgussverfahren her. Wir nutzen praktisch dieselbe Ausrüstung für das Zusammenfügen gegossener Bauteile. Und wir fühlen uns auch denselben hohen Standards im Hinblick auf Qualität und operative Leistungsfähigkeit verpflichtet. Unsere Märkte mögen unterschiedlich sein, doch der Fertigungsprozess ist im Wesentlichen identisch.
Welche Vorteile hat die neue Division?
Mit der Zusammenführung von Mixpac und Geka können wir die Beschaffung von Maschinen, Werkzeugen und Formen bündeln und Kosten einsparen. Ein weiterer Vorteil ist die geografische Präsenz. Geka ist mehrheitlich in Europa sowie Nord- und Südamerika aktiv. Mixpac hingegen hat eine starke Stellung in der Schweiz und in China. Die beiden Unternehmen ergänzen sich somit punkto Standorten in idealer Weise. So bietet die Geka-Niederlassung in Brasilien den Mitarbeitenden von Mixpac eine gute Ausgangsbasis, um den dortigen Dentalmarkt zu erschliessen. Der Standort von Mixpac in China erlaubt es Geka wiederum, Spritzgussformen in China zu beschaffen.
Kurz gesagt: Unsere neue Division Applicator Systems ist der branchenweit grösste und einzige globale Player. Dies ist ein entscheidender Vorteil, zumal unsere Kunden weltweit dieselben Produkte nachfragen.
Was können Sie uns zum Portfolio der neuen Division Applicator Systems sagen?
Wir sind ein Anbieter von Produkten und Services für das Applizieren und Mischen von Flüssigkeiten im Bereich Klebstoffe sowie für die Dental-, Gesundheits- und Schönheitsbranche. Dazu zählen Produkte für präzise Applikationen sowie Misch- und Auftragssysteme für ein und zwei Komponenten. So entwickeln und fertigen wir für die Automobilbranche Applikatoren für Klebstoffe zur Montage von Windschutzscheiben, für die Dentalbranche Applikatoren für das Anbringen von Füllungen und für die Kosmetikindustrie Produkte wie Mascaras, Lipgloss und Eyeliner.
Welche Pläne haben Sie für APS?
Kurz und knapp: Wir wollen profitabel wachsen. Unser Umsatz betrug 2017 rund CHF 420 Millionen. Diese Zahl wollen wir in wenigen Jahren auf CHF 800 Millionen bis CHF 1 Milliarde steigern. Wie wollen wir das erreichen? Durch die Akquisition von Unternehmen, aber auch indem wir das bestehende Geschäft weiterentwickeln. So bauen wir im Rahmen unseres Kosmetikgeschäfts den Standort Bechhofen, Deutschland, auf die doppelte Grösse aus. Zudem errichten wir in Polen ein neues Werk, um unser Industriegeschäft voranzutreiben. In den Nischenmärkten mit hohen Anforderungen bleiben wir engagiert, damit wir unsere solide Profitabilität halten können.
Was ist den Kunden im Applikatorgeschäft wichtig?
In Zukunft dürfte es immer wichtiger werden, wie die verschiedenen Materialien aufgetragen werden. Heute wählt der Kunde für gewöhnlich das Applikatorsystem und kauft anschliessend die dafür geeigneten Klebstoffe sowie Versiegelungs- und Füllmittel. Deshalb werden Zweckmässigkeit, Qualität und Leistung der Applikatorsysteme zunehmend wichtigere Verkaufsargumente. Aber letzten Endes hängt unser Erfolg davon ab, dass wir unseren Kunden das jeweils richtige System in Bezug auf Inhalt und Anwendung anbieten können. Aus diesem Grunde verbessert APS laufend ihre Testkapazitäten für unterschiedliche Kombinationen und Lösungen, damit wir unseren Kunden das jeweils am besten für ihre Bedürfnisse geeignete Auftragssystem empfehlen können.
Sulzer investiert in additive Fertigungstechnologien (AM). Welche Rolle spielen AM in Ihrer Division?
Die additive Fertigung gewinnt zusehends an Bedeutung. So setzen wir seit einigen Jahren 3D-Drucktechnologien für die Fertigung von Prototypen von Mascara-Bürsten ein. Mittlerweile sind neuartige Materialien und Methoden auf dem Markt und die Technologie ist erschwinglicher geworden, sodass wir die AM zu gegebener Zeit für Massenproduktion nutzen können.
Mit neuen Materialien und Technologien experimentieren
Die Forschungsabteilungen entdecken laufend neue Materialien, die sich für das 3D-Druckverfahren eignen. Noch sind die Verfahren kostenintensiv und werden daher nur für die Herstellung von Prototypen oder Bauteilen in geringen Stückzahlen eingesetzt. Geka nutzt die 3D-Drucktechnologie zur Herstellung von Prototypen für Mascara-Bürsten seit 2007.
Mit dem neuen Kunststoff und dem neuen Fertigungsverfahren konnten unsere Produktentwickler den Entwicklungsprozess von Prototypen für Mascara-Bürsten erheblich beschleunigen. Unsere Produkte können nun viel schneller eingeführt werden und treffen die Kundenbedürfnisse noch besser.
Amaury de Menthiere Divisionsleiter Applicator Systems
Zur Beschleunigung des Entwicklungsprozesses suchte das Forschungsteam nach alternativen Methoden und Materialien für die Prototypherstellung. Und es wurde fündig: Ein neuartiger Kunststoff kam auf den Markt. Dieser spezifische Kunststoff gewährleistet, dass jede einzelne Borste stabil genug ist, um die Wimpern zu trennen, aber auch elastisch genug, um das Auge nicht zu verletzen.
Nachdem das Material gefunden worden war, musste noch das passende Produktionsverfahren bestimmt werden. Die Teams unternahmen zahlreiche Versuche, um das beste Herstellungsverfahren zu evaluieren. Man entschied sich letztlich für ein additives Fertigungsverfahren, das als selektives Lasersintern (SLS) bezeichnet wird.
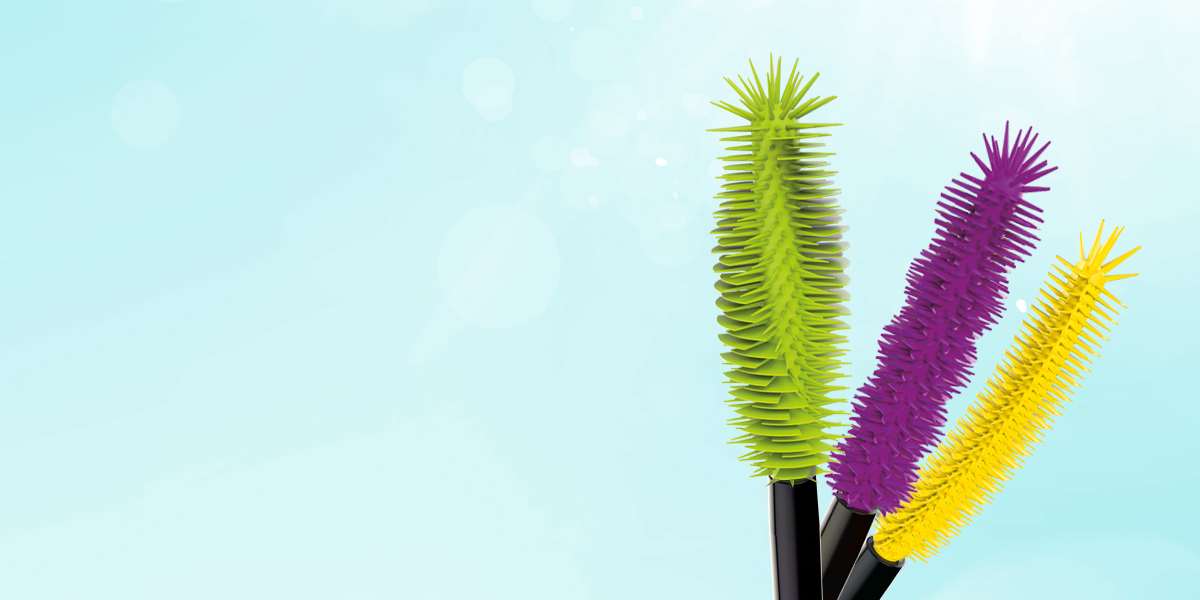
Wie funktioniert selektives Lasersintern?
Beim selektiven Lasersintern (SLS) handelt es sich um eine relative junge Technologie für die additive Fertigung. Bisher wurde sie bei Sulzer hauptsächlich für die rasche Herstellung von Prototypen und Bauteilen in kleiner Stückzahl genutzt. Je weiter sich die additive Fertigung entwickelt, desto vielfältiger werden die industriellen Anwendungen für die SLS-Technologie.
Eine Lasersinteranlage trägt eine dünne Schicht pulverförmigen Materials auf eine Bauplattform auf. Mithilfe eines Laserstrahls und eines beweglichen Spiegels wird das Material selektiv verschmolzen. Nach dem Absenken der Bauplattform wird die nächste Pulverschicht aufgetragen. Dieser Vorgang wird wiederholt, bis das Bauteil – Schicht um Schicht – im Pulverbett aufgebaut wurde. Diese Technologie hat indes den kleinen Nachteil, dass die Bauteile nicht die exakt gleiche Oberflächenstruktur wie Spritzgussteile aufweisen.
Funktionsprinzip des SLS-Prozesses.
Verkürzung der Produktionszeit um 17 Wochen
Mit der neuen Methode gelang es Sulzer, den Entwicklungsprozess erheblich zu beschleunigen. Anstatt 18 Wochen auf einen Prototyp zu warten, hält der Kunde diesen bereits nach einer Woche in den Händen. Und dank des neuartigen Materials kann der Kunde die Bürste im praktischen Schminktest einsetzen. Falls es noch kundenspezifischer Zeichnungsanpassungen bedarf, können diese unmittelbar vorgenommen und die neue Bürste mittels 3D-Druck angefertigt werden.
dauert es dank unseres innovativen Verfahrens, bis der Kunde den Prototypen in den Händen hält.
Noch sind Qualitätsunterschiede zwischen den Prototypen erkennbar, die mit dem 3D-Druck- beziehungsweise dem Spritzgussverfahren hergestellt wurden. Die Oberfläche der 3D-gedruckten Bürsten ist anders als bei den Spritzgussteilen. Und auch die Übertragungsmenge der Mascara-Masse kann abweichen. Aber was zählt: Der Kunde kann anhand der Prototypen ausreichend genaue Ergebnisse ableiten, um Entscheidungen zu treffen.
Der Entwicklungsprozess ist schneller und die Produkte kommen rascher auf den Markt. Überdies erfüllt das Endprodukt die spezifischen Anforderungen des Kunden noch besser.
Die neue Technologie macht rasch Fortschritte. In absehbarer Zeit werden additive Fertigungsverfahren nicht nur zur Prototypenherstellung verwendet werden, sondern auch in den Fabrikhallen von Sulzer Einzug halten.
Sind Sie an weiteren Storys über unsere Produkte und Services interessiert? Lesen Sie mehr auf www.sulzer.com/stories-de.