Die Zukunft der Laufrad-Herstellung
Sulzer und ein namhafter Kompressorenhersteller entwickeln gemeinsam einen innovativen Herstellungsprozess für die Fertigung geschlossener Laufräder. Das neue Produktionsverfahren erlaubt es Sulzer, Teile in höchster Qualität bei radikal kürzeren Vorlaufzeiten herzustellen. Wir haben das ehrgeizige Ziel, geschlossene Laufräder innerhalb von 48 Stunden an unsere Kunden liefern zu können.
Beim Laufrad handelt es sich um ein rotierendes Pumpenbauteil. Es überträgt Energie vom Motor zur Flüssigkeit und versetzt diese in Strömung, um Druck aufzubauen. Im Gegensatz zu einem offenen Laufrad ist beim geschlossenen Laufrad an der Vorderseite eine Deckscheibe angebracht.
Aufgrund ihrer besonderen Geometrie konnten geschlossene Laufräder für Pumpen bisher nur im Gussverfahren hergestellt werden. Doch dieses Verfahren birgt die Gefahr kleinerer Mängel im oder an der Oberfläche des Materials sowie geringfügiger geometrischer Abweichungen. Auch sind der Qualität der Oberflächenbeschaffenheit Grenzen gesetzt. Dies kann die Leistung des Laufrads beeinträchtigen, sodass unter Umständen Nachbearbeitungen wie umfangreiches Auswuchten oder eine Oberflächenbehandlung notwendig werden.
Ein weiterer Nachteil, der auch auf das sogenannte Rapid Casting zutrifft, sind die relativ langen Lieferzeiten.
Kombination von additiven und subtraktiven Technologien
Deshalb kommt in der Laufradherstellung zukünftig ein schon seit vielen Jahren verwendetes Verfahren zur Anwendung: Laserauftragsschweissen, auch bekannt als Laser Metal Deposition (LMD). Der Schlüssel hierbei ist, LMD für den additiven Aufbau der 3D-Geometrie einzusetzen und danach mit klassischem 5-Achs-Fräsen eine qualitativ hochwertige Oberflächenbeschaffenheit und hohe Präzision zu erreichen.
Dieser hybride Prozess hat für gewisse Branchen, darunter auch die Pumpenindustrie, sogar noch mehr Vorteile als das allgemein bekannte selektive Laserschmelzen (Selective Laser Melting, SLM – auch als 3D-Metalldruck bezeichnet). Die Auftragsrate ist rund eine Grössenordnung (5–15-mal) höher als beim klassischen SLM-Verfahren. Gleichzeitig lässt sich die für ein Bauteil benötigte Menge an additivem Material signifikant reduzieren, was die Herstellungskosten senkt. Auch kann auf das Anbringen von Stützstrukturen verzichtet werden. Mit modernsten 5-Achs-Fräsen lassen sich zudem eine sehr hohe Präzision und Oberflächenqualität erzielen. Überdies sind bei einer hybriden Fertigung die Produktentwicklungszyklen noch kürzer, da zunächst ein Prototyp hergestellt werden kann, der ein rascheres Kundenfeedback ermöglicht.
Wie funktioniert die hybride Fertigung?
Beim konventionellen Fertigungsprozess, auch als subtraktive Herstellung bezeichnet, wird Material von einem Schmiedestück oder Gussteil entfernt. Bei der additiven Fertigung, auch als 3D-Druck bekannt, wird das Material computergesteuert Schicht um Schicht zu einem dreidimensionalen Produkt aufgebaut. Die hybride Fertigung kombiniert beide Produktionsverfahren.
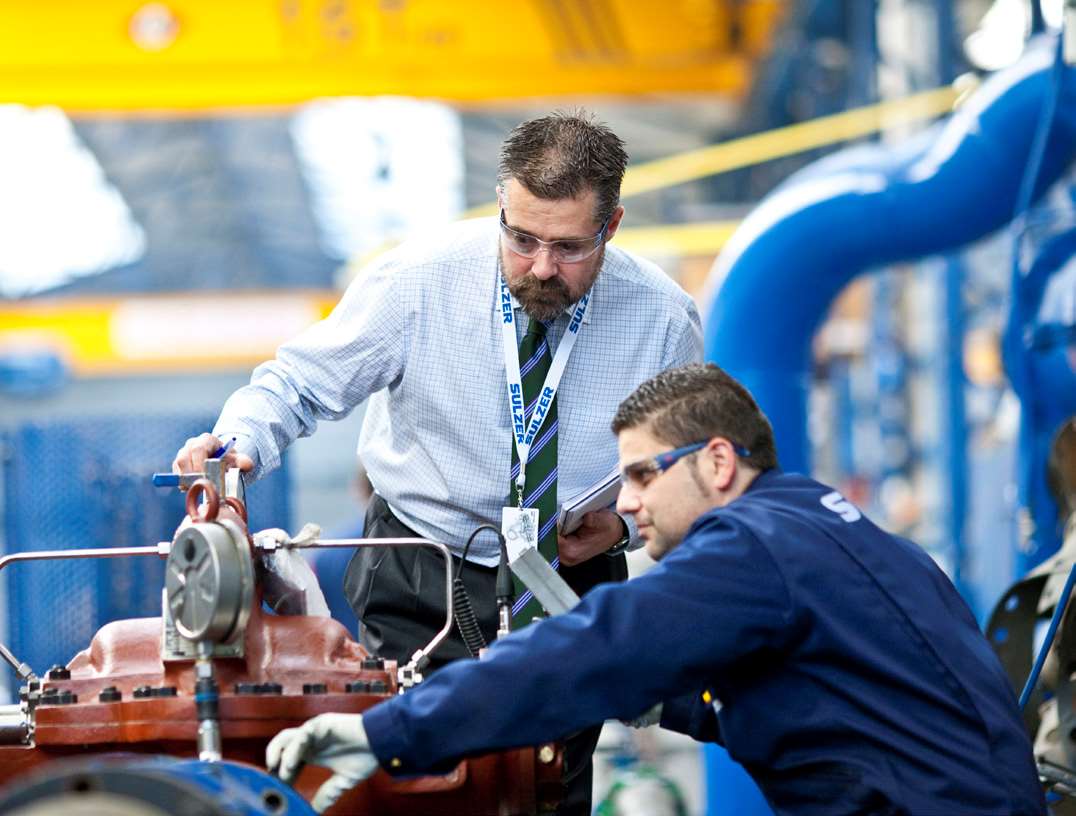
Additive und subtraktive Prozesse werden von ein und derselben Werkzeugmaschine ausgeführt. Am Anfang unseres Hybridprozesses zur Laufradherstellung, für den bereits ein Patent angemeldet wurde, steht ein kleiner Stangenabschnitt, der mittels einer 5-Achs-Fräse zu seiner endgültigen Form abgespant wird. Diese Bearbeitung ist nur möglich, weil der Aussendurchmesser dieses Kernteils kleiner als das herzustellende Laufrad ist. Somit können die Fräswerkzeuge sämtliche Kanäle erreichen. Sobald der Kernteil des Laufrades fertiggestellt ist, wird die verbleibende Laufradgeometrie mittels LMD-Technologie radial aufgebaut. Das aufgebrachte Material wird anschliessend abgefräst, bis es seine endgültige Form und Oberflächenqualität erreicht hat. Abhängig von der Werkzeugzugänglichkeit lassen sich dieser additive Schritt und das abschliessende Fräsen mehrere Male wiederholen, bis das Laufrad seinen vorgesehenen Durchmesser aufweist.
Funktionsprinzip des Hybridfertigungsverfahrens, eine Kombination subtraktiver und additiver Herstellung.
Geschlossene Pumpenlaufräder in nur 48 Stunden
Um den Prozess zu verbessern, gilt es, sämtliche Parameter, d.h. Laserleistung, Pulverzufuhr, Geschwindigkeit, Fokussierung usw., zu optimieren. Auch die CAM-Software-Tools (CAM = computer-aided Manufacturing) müssen so eingerichtet werden, dass sie die Vorteile der hybriden Fertigungsprozesse nutzen können. Die meiste CAM-Software ist indes für die subtraktive Fertigung programmiert. Der additive Auftrag von mehr als einer Schicht ist erst seit Kurzem notwendig geworden, insbesondere dann, wenn der Materialauftrag im LMD-Verfahren geschieht.
Für die Parameteroptimierung und Automatisierung der Werkzeugpfadprogrammierung schloss sich Sulzer mit einem namhaften Kompressorenhersteller zusammen. Beide Unternehmen zeichnen sich durch Hingabe und Erfahrung aus – Qualitäten, aufgrund derer sie ihr ehrgeiziges gemeinsames Ziel bis Mitte 2018 erreichen werden: geschlossene Laufräder mit höchsten Qualitätsstandards innerhalb von 48 Stunden ausliefern zu können. Dies würde eine erhebliche Verkürzung gegenüber der bislang beim traditionellen Gussverfahren üblichen Herstellungszeit von 25–35 Tagen bedeuten.
Hybride Fertigungsprozesse für andere Komponenten
Die hybride Fertigung beschränkt sich indes nicht auf Laufräder oder einzelne Werkstoffe. Deshalb gibt es bereits Bestrebungen, auch andere Pumpenteile mittels Hybridverfahren herzustellen oder Komponenten aus verschiedenen Werkstoffen aufzubauen. Ein Beispiel für die Anwendung unterschiedlicher Werkstoffe bei der Fertigung ist das Aufbringen einer verschleissresistenten Beschichtung mittels LMD. Die Beschichtung kann im Laufrad einen Verschleissring ersetzen.
Additive Fertigung von Sondergrössen und -formen
Sulzer stellt kleine statische Mischer mit der additiven Fertigungsmethode her. Damit kann das Unternehmen Designanpassungen vornehmen und Sondergrössen und -formen effizienter herstellen.
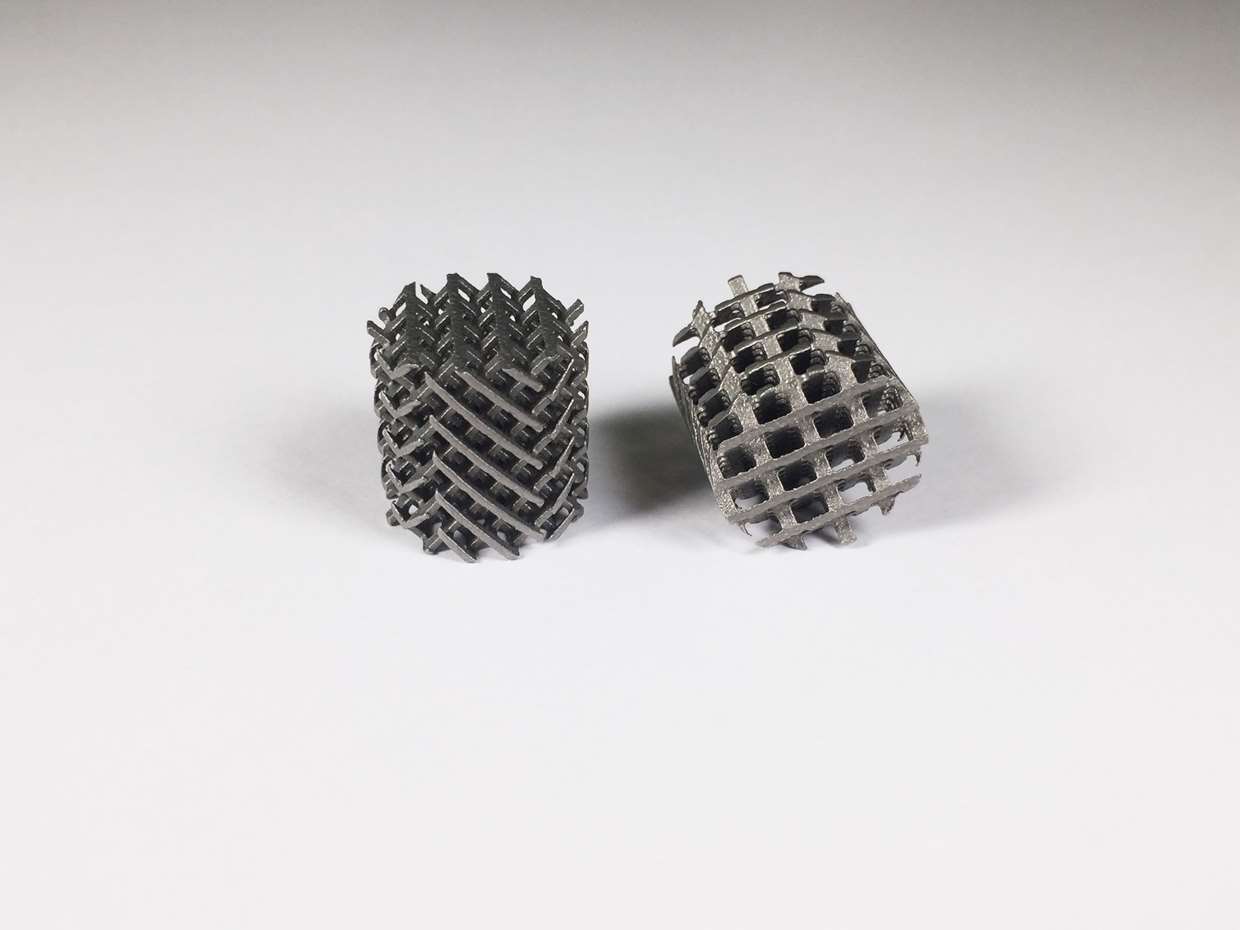
Statische Mischer werden in Rohren oder Schächten installiert. Sie haben keine beweglichen Teile und sorgen für spezifische Misch- und Dispersionseffekte in kontinuierlichen Prozessen. Die Mischer von Sulzer kommen in der Faserherstellung, Polymertechnologie, Wasseraufbereitung sowie in der chemischen und der Lebensmittelindustrie zum Einsatz.
Langjährige Erfahrung mit additiven Fertigungsmethoden
Schon vor zehn Jahren nutzte die Division Chemtech selektives Lasersintern (SLS) zur Herstellung kleiner statischer Mischer. Additive Herstellungsverfahren kamen beispielsweise vielfach in der Entwicklung des SMX-plus-Mischers und des SMR-plus-Wärmeaustauschers zur Anwendung. Mit SLM hergestellte Elemente für statische Mischer wurden früher – und teilweise noch heute – für Kunden angefertigt, deren Mischer spezielle Ausmasse oder Formmerkmale aufwiesen. Das Haupteinsatzgebiet für SLM ist jedoch die Herstellung von Prototypen, Halterungsteilen sowie Teilen und Werkzeugen in kleinen Serien. Das Verfahren ist noch zu kostspielig, um für die Massenproduktion eingesetzt zu werden.
Wie funktioniert Selective Laser Melting (SLM)?
Eine SLM-Maschine verteilt eine dünne Schicht von Metallpulver auf eine Grundplatte. Ein Laser, der von einem beweglichen Spiegel gelenkt wird, schmilzt das Pulver Schicht um Schicht.
Funktionsprinzip des SLM-Prozesses.
Sind Sie an weiteren Storys über unsere Produkte und Services interessiert? Lesen Sie mehr auf www.sulzer.com/stories-de.