The next generation of impeller manufacturing
Sulzer and a well-known compressor manufacturer are co-developing an innovative manufacturing process for closed impellers. Thanks to the new process, Sulzer will be able to offer high-quality parts with radically low lead times. The ambitious goal is to offer closed impellers within 48 hours to our customers.
An impeller is the rotating component of a pump. It transfers the energy from the motor to the fluid and accelerates the fluid to build up pressure. In contrast to an open impeller, a closed impeller additionally has a front shroud attached to it.
Because of the unique geometry of closed pump impellers, the only way to produce these components to date has been to use casting technologies. However, with these technologies there are risks of small internal and surface defects, fair-but-limited surface quality, and slight geometrical inaccuracies. These issues not only affect the overall performance of the part but also determine how much post-processes – like surface treatment and balancing – are necessary.
Another factor, even for so-called rapid casting technologies, is the relatively long lead time to produce a finished part.
Combining additive and subtractive technologies
The solution to much faster and better impeller production lies in a technology that has been used by Sulzer for many years already – laser metal deposition (LMD). The key is to use LMD to build up 3D geometries additively, then to use classic 5-axis milling to achieve high-quality surfaces and accuracy.
The hybrid process brings even greater advantages than the widely known selective laser melting process (SLM) – often referred to as 3D metal printing – to certain industries, including the pump industry. The deposition rate is about one magnitude (5–15 times) higher than classic SLM. At the same time, the amount of additive material within a component can be significantly reduced, which keeps the overall process cost reasonable. Further, support structures for additive buildups can be avoided. The state-of-the-art 5-axis milling process achieves high precision and surface quality. Hybrid manufacturing also makes our product development cycles faster because we can produce prototypes and get feedback from customers much faster.
How hybrid manufacturing works
In the conventional machining process, also called subtractive manufacturing, material is removed from a bar, forging, or casting. In additive manufacturing, also known as 3D printing, layers of material are formed one by one under computer control to create a three-dimensional object. Hybrid manufacturing combines additive and subtractive production technologies.
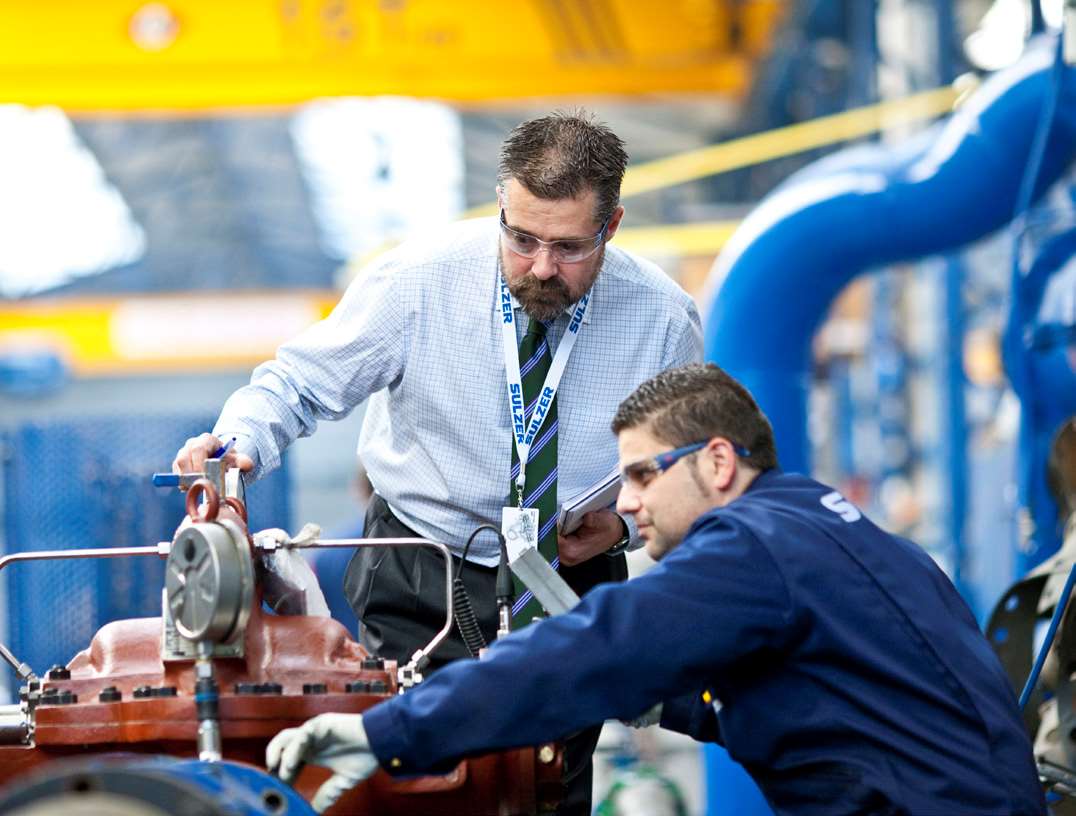
Additive and subtractive manufacturing are combined in one machine tool. The patent-pending hybrid production process for a closed impeller starts with a small wrought billet, which is machined to its final geometry with 5-axis milling operations. This milling step is only possible because the radial dimension of this core part is smaller than the size of the final impeller. Thus, all channels are accessible with milling tools. When the impeller core is finished, the remaining geometry for the final impeller is radially built up via laser metal deposition (LMD). The added material is then milled to the final geometry and surface quality. Depending on tool accessibility, this additive step with subsequent final machining can be repeated several times in order to grow the impeller radially to its final diameter.
Functional principle of hybrid manufacturing, the combination of subtractive and additive manufacturing.
Closed pump impellers in 48 hours
To improve the process, all involved parameters like laser power, powder feed, speed, focal position, etc. need to be optimized. In addition, CAM (computer-aided manufacturing) software tools need to utilize the capabilities of such hybrid manufacturing processes. Most CAM software is programmed to fulfill subtractive manufacturing tasks. The additive generation of more than just a coating layer – especially in the way the LMD process adds material – only recently became a requirement.
To optimize the parameters and to automate the toolpath programming, Sulzer joined forces with a well-known compressor manufacturer. With the dedication and experience of both companies, the teams are convinced that they will be able to achieve their ambitious common goal of offering high-quality closed impellers within 48 hours to customers starting in mid-2018. This is a radical drop from the current standard of 25–35 days of production time using traditional casting methods.
Applying hybrid manufacturing to other parts
Hybrid manufacturing is neither limited to impellers alone nor to single materials. Therefore, future developments aim to use hybrid manufacturing for other pump components or to use different materials within one part. One example of the use of different materials is the application of a wear-resistant coating via LMD during the manufacturing process. This coating can be applied in the respective impeller area to replace an impeller wear ring.
Additive manufacturing for unusual sizes and features
Sulzer has created small-scale static mixers using additive manufacturing. In this way, the company was able to make design adjustments and to produce unusual sizes and features more efficiently.
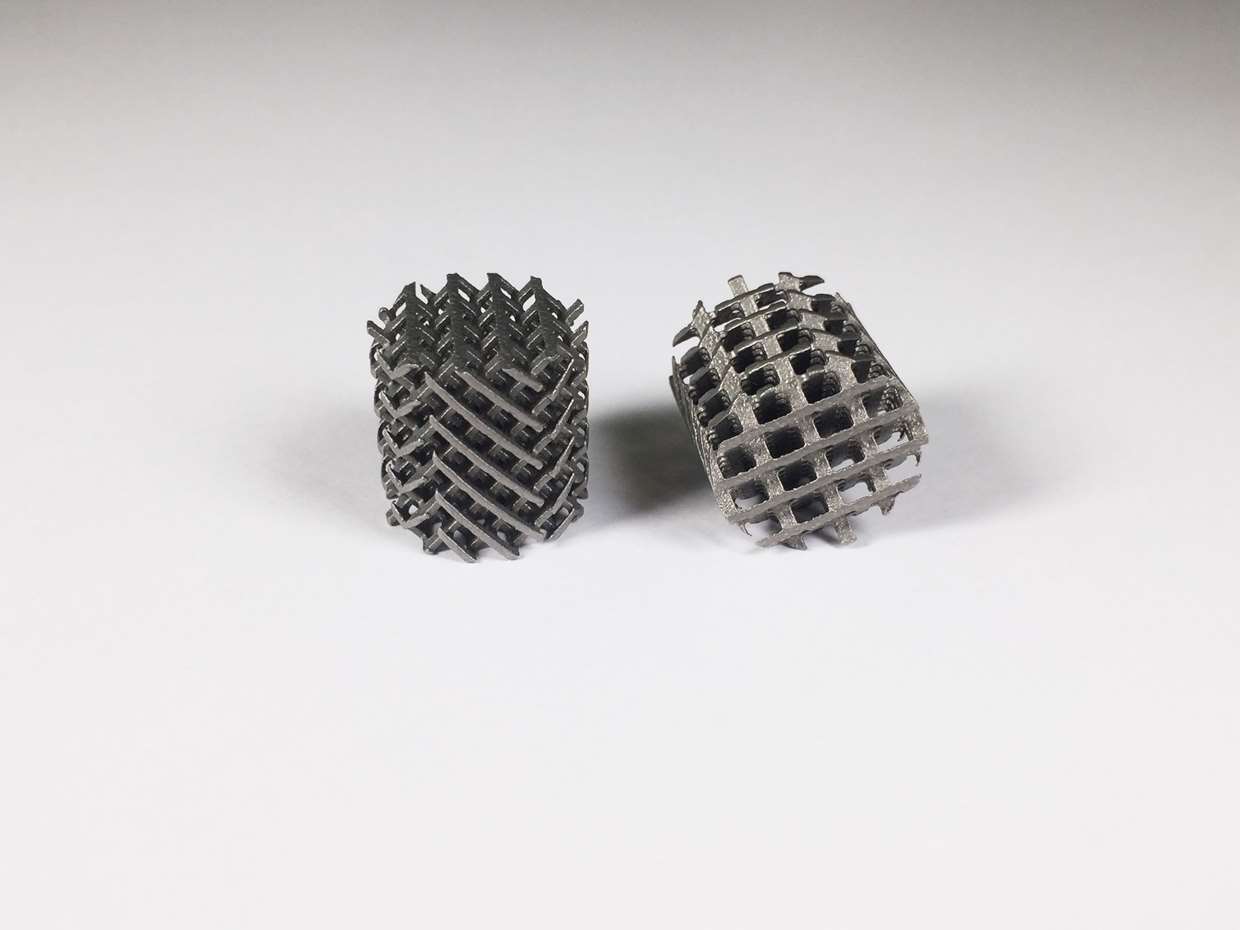
Static mixers are mixing elements installed in a pipe or duct. They function without moving parts and are used to achieve specific mixing and dispersion in continuous processes. Sulzer produces mixers for the fiber production, polymer technology, water treatment, chemical, or food production industries.
Long-time experience with additive manufacturing
Already ten years ago, the Chemtech division used selective laser sintering for small-scale static mixers. Additive manufacturing was, for example, used a lot for the development process of the SMX plus mixer and the SMR plus heat exchanger. Static mixing elements made by selective laser melting (SLM) have been and still are occasionally manufactured and sold to customers for cases requiring unconventional sizes or features. The main application area of SLM is for prototyping, to produce support parts, small batch size parts, or tools. At the moment, it is still too expensive for mass production.
How selective laser melting (SLM) works
A laser melting machine distributes a thin layer of metal powder onto a build platform. The powder is melted layer by layer with the help of a laser that is directed with a flexible scanning mirror.
Functional principle of the selective laser melting process, also called SLM.
Interested in more stories about our products and services? Check them out at www.sulzer.com/stories.