Sulzer’s future factories: smart and learning
The fourth industrial revolution is not only about new technologies, it is about changing the way of doing business and winning through information. Sulzer has reorganized its pumps engineering, manufacturing, and supply chain into an integrated global factory network. Each element of the network will be smart and contribute to constant learning. In this way, we will be able to cut delivery times and offer Sulzer’s recognized quality at competitive prices at the same time.
Through the ages, the world has seen many technological revolutions. We are living in the digital age, and markets are changing faster than ever before. Companies are reinventing their business models for tomorrow.
Sulzer is reorganizing and digitally enabling its global pumps manufacturing and supply chain network.
From isolated shops to a network of focused factories
Digitalization has enabled Sulzer to set up a connected factory network.
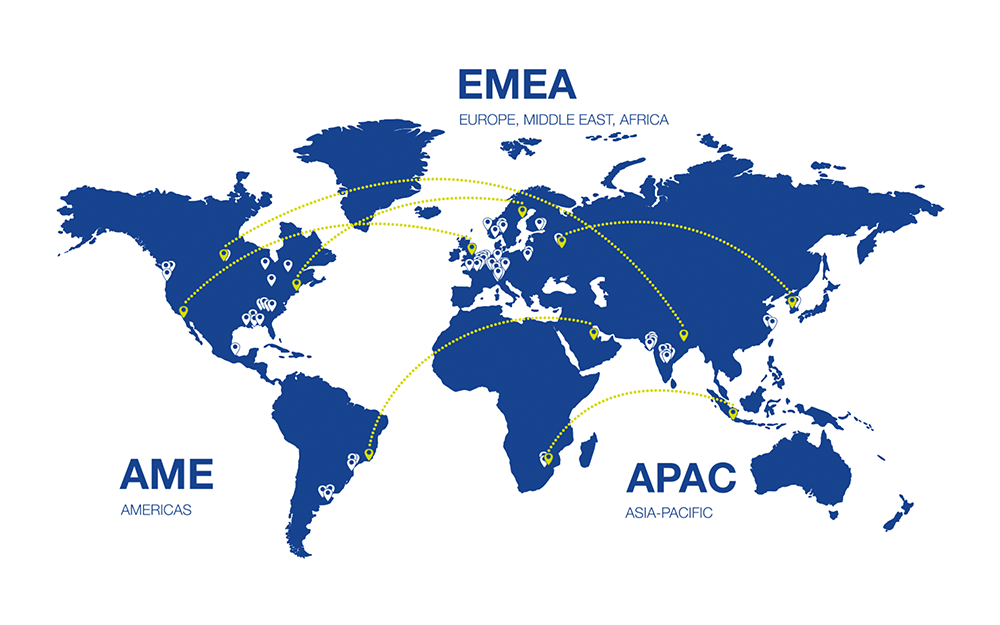
Sulzer has converted its network from insular factories that all operated fairly autonomously to a connected factory network that can be managed virtually. This change brings many advantages both for customers and for Sulzer:
- Speed: We can prevent local bottlenecks in the network and, thus, reduce our lead times. It takes considerably less time from the beginning of a project to its completion, and delivery of products is faster.
- Cost: We can offer our products at competitive prices because we can tap into regional cost advantages within the customer sourcing restrictions.
- Proximity: We are close to our customers and can manufacture products regionally because we have at least one factory for every delivery model type in every region.
-
Traceability: When required, we can trace back every detail about the pump: where its components came from, where it was assembled, who the suppliers were, and so on.
Four virtual factory families
In the past, each Sulzer factory manufactured several different pump types. It worked more or less autonomously and had its own order pipeline, supply chain, and processes.
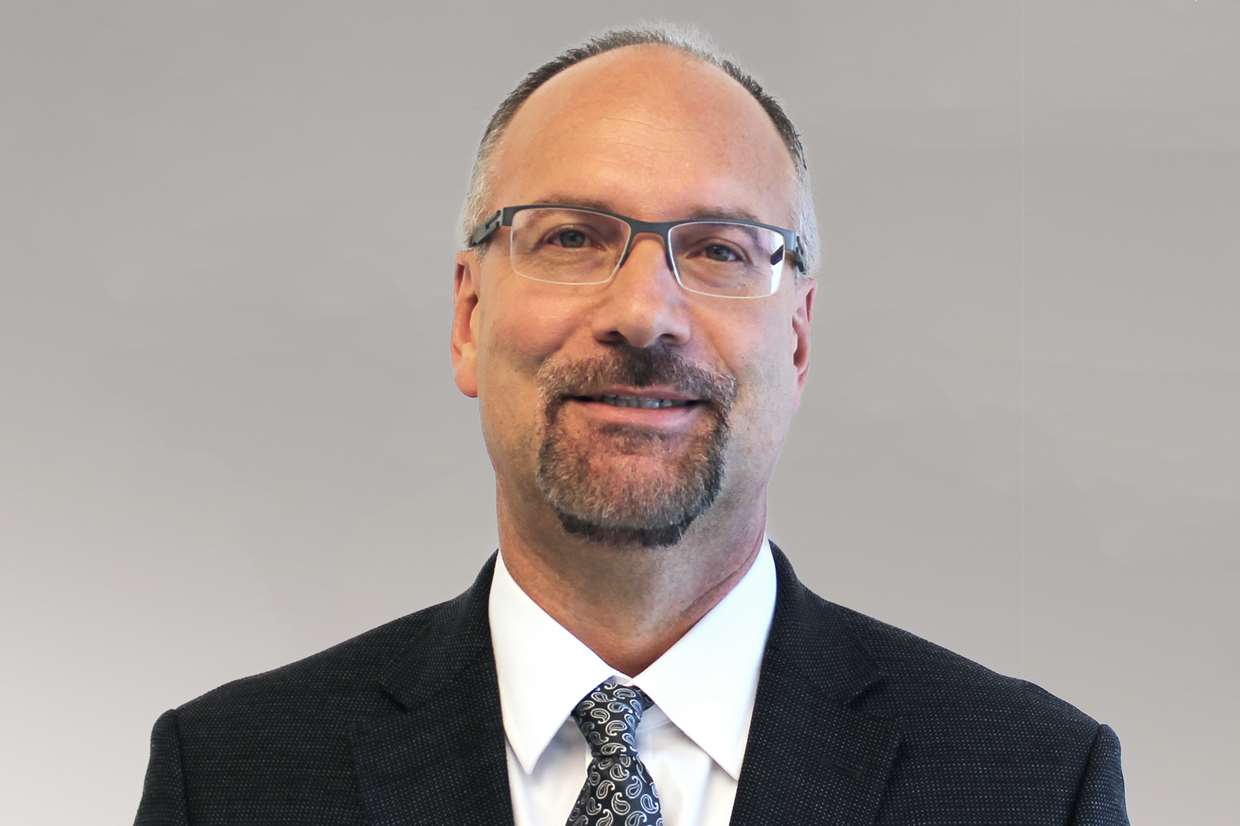
Digitalization is changing the way we do business. It influences our products, our fabrication, and our business processes. And this is just the beginning.
Robert Laflamme Head Global Operations
We have now organized our factories around the world into factory families according to our four different delivery models: standard, configured, pre-engineered, and engineered pumps. One factory family consists of all factories that manufacture the same pump types and work to the same processes. The four families can be managed in real time and on a global level – virtually like four factories.
This allows us to fulfill the different customer needs in an ideal way: speed (reduced delivery time), competitive prices, customer proximity, and traceability of products and components. All factories around the globe will fully live up to common Sulzer quality standards.
Furthermore, the new setup allows us to balance the workload among the factories, to stimulate help and exchange within each factory family, and to roll out new improvements quickly around the world.
Humans and robots working together side by side
Better fulfilling our customer demands and becoming more competitive to grow our business are at the core of Sulzer’s digital strategy. Pump manufacturing has many complex steps, but many are also simple and repetitive. With the advances in sensors, collaborative smart robots (“cobots”) are gradually becoming cost-effective.
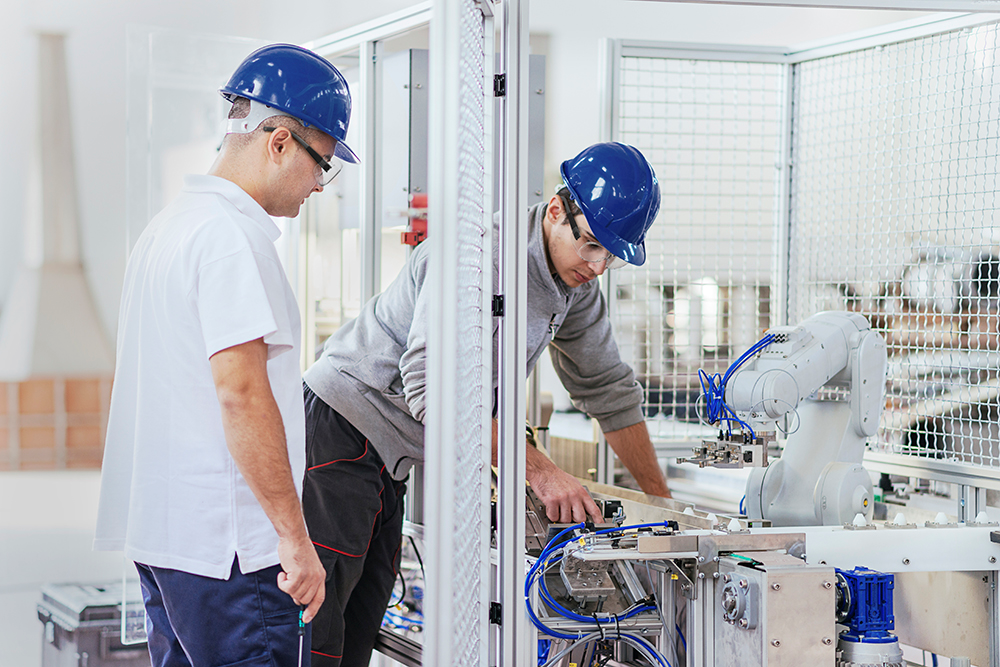
This is also true for our industry, especially with regard to small pumps. The cobots are designed to work in line or even side-by-side with humans. So, we can selectively enhance our production to offload simple tasks or to assist with non-ergonomic tasks. These cobots are connected to our central systems.
To globally manage all the information for operations and for improvements, Sulzer is aligning and integrating the software tools that are used around the world. From requirements management to computer-aided design (CAD), computer-aided engineering (CAE), computer-aided manufacturing (CAM), and planning to manufacturing execution system (MES) – everything is managed in a seamless digital toolchain.
Our smart and learning factories will make us a faster and better partner for our customers. They will create exciting new opportunities for our employees. They will drive growth and increase cost competitiveness for our shareholders.
Bringing digitalization to the shop floors
Digitalization is not only vital when it comes to managing the factory network, it will also bring improvements on the shop floor level.
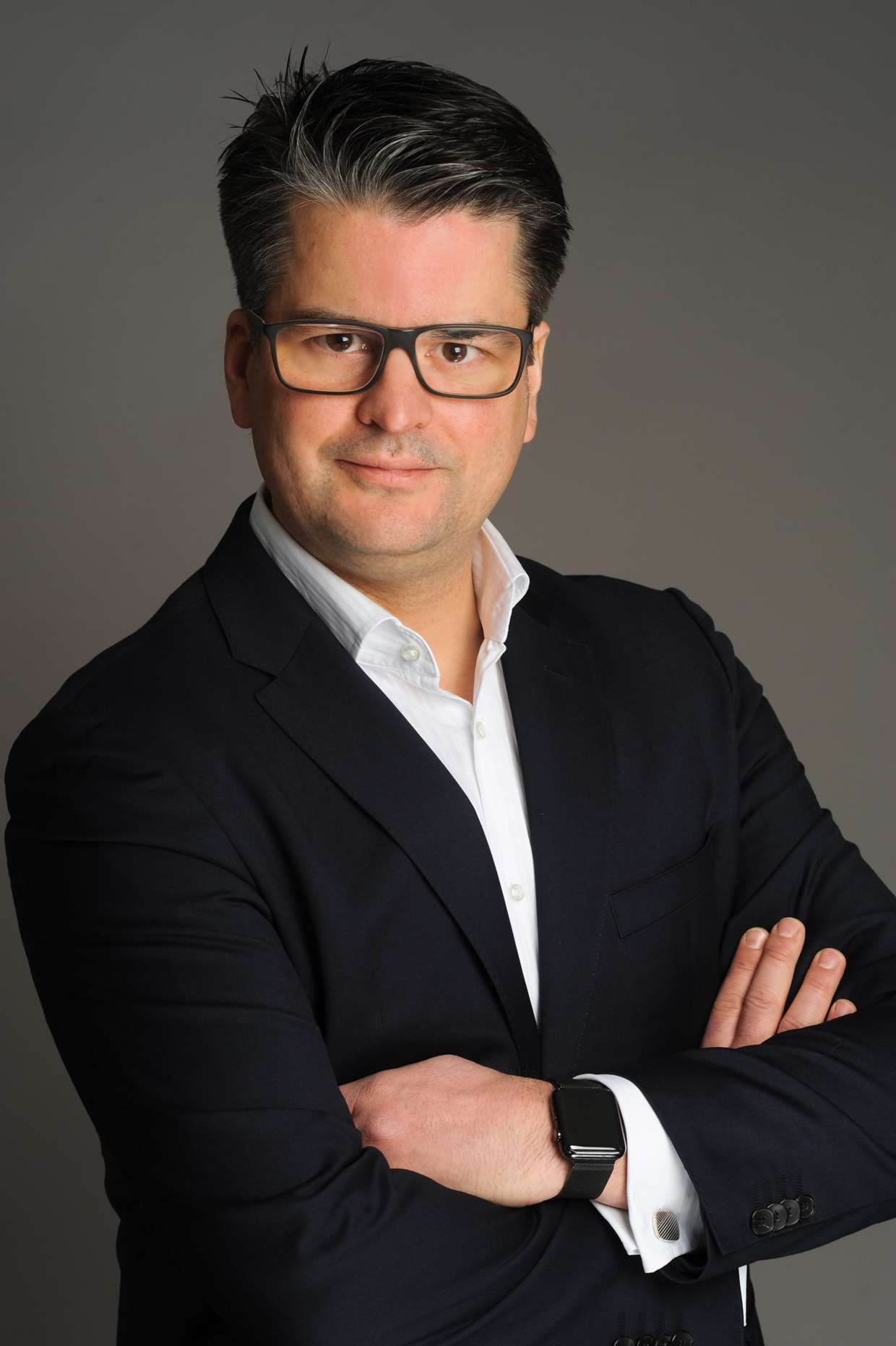
With smart factories, we will be able to flexibly adapt our products, our suppliers, our technologies, and our manufacturing network to better satisfy customer and market demands.
Enno Danke Head Global Manufacturing Technology
Especially in the engineered pumps business, which has low volumes and high variance, the traditional way of manufacturing with only limited automation still predominates. Each project is tailored to the customer. Hence, the process steps are not usually repetitive, the tools used are not typically connected, and issues are typically resolved through direct interaction of experts from different departments. So, improvements rely on singular analysis and suggestions of our employees who cannot tap into a regular pool of structured information.
Making data accessible and understandable
The foundation for fast learning and improvement is the right information. So we can have structured real-time data available at every process step, we are connecting our machine tools, deploying connected manual tools, and setting up touch screens at the different workplaces on the shop floors.
The paperless factory gives real-time feedback on the work center status because the production orders are digitally started, routed, and confirmed. Our technicians can easily record the reasons and amount of time they spend solving issues and waiting. They can access digital models and work instructions to overcome ambiguities. Also, they can easily connect to experts in other functions without always having to call for a physical meeting.
All the data collected needs then to be aggregated, put into context, and analyzed for us to continually improve. Thus, analytical and creative capabilities are becoming more important. We are investing in our Sulzer Production System team to stimulate and support the organization with this.
Interested in more stories about our products and services? Check them out at www.sulzer.com/stories.