– Focus – Sustainable and degradable bioplastics with Sulzer
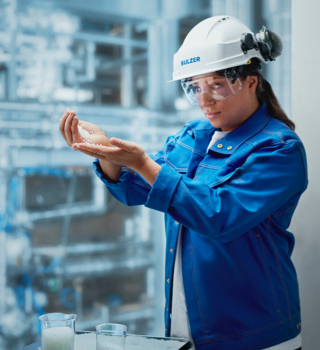
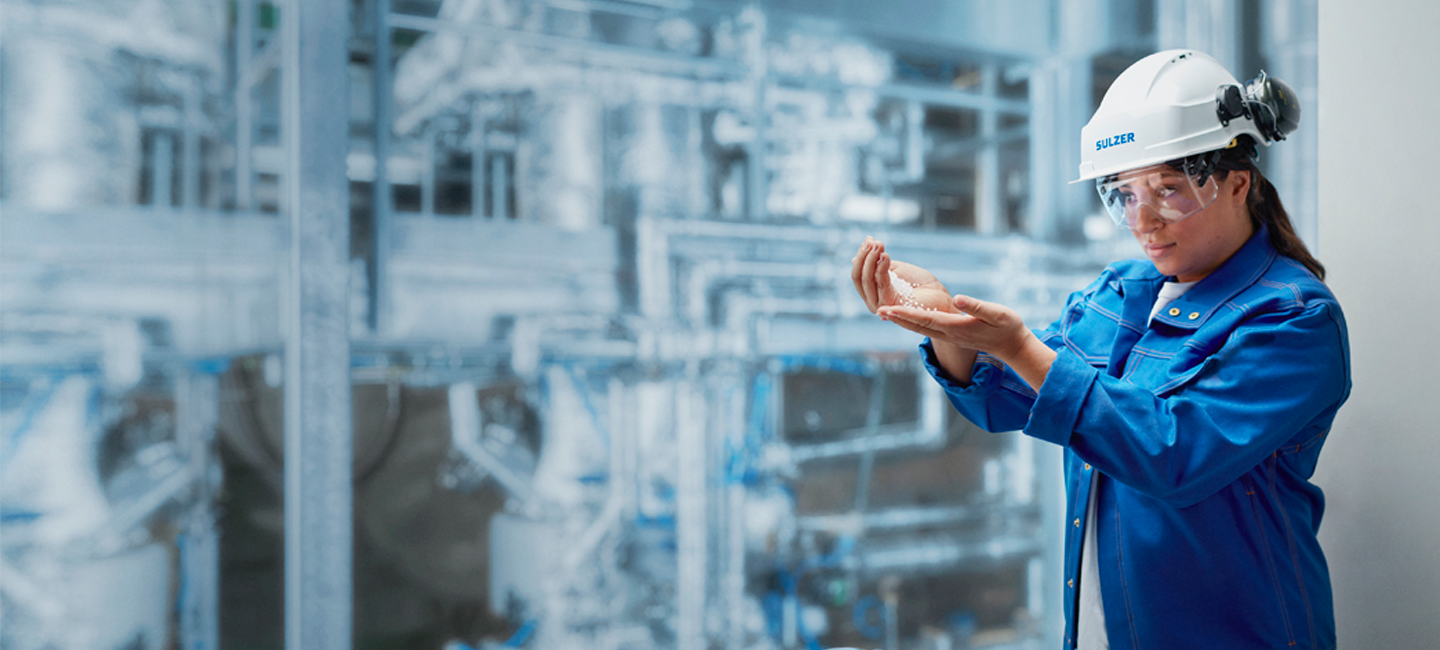
Sustainable and degradable bioplastics with Sulzer
While we have come to realize the environmental limitations of plastics, there is still a great future in such materials — especially if solutions based on the principles of renewability and circularity are adopted. One of the most remarkable examples is polylactic acid (PLA), a highly sustainable bioplastic that is now produced worldwide. PLA production is mostly based on Sulzer Chemtech’s advanced technology, which is included in almost all PLA production plants currently in operation across the globe.
In just over 60 years, plastics have witnessed an extraordinary evolution as materials, fitting practically any application. From consumer goods to packaging, all the way to art and medicine, plastics are ubiquitous. Thanks to their adaptable properties and limited cost, no other alternative can effectively compete.
However, these tremendous advantages typically come with an environmental price tag that is impossible to overlook. Traditionally made from fossil fuel-based petrochemicals, they rely on non-renewable resources. In addition, they are generally not easily recyclable, and it can take anywhere from 20 to 500 years for them to decompose. In this time, the waste accumulates and can leach unwanted chemicals, with disastrous environmental consequences. At least 14 million tonnes of plastic end up in the oceans every year, and plastic makes up 80% of all marine debris found from surface waters to deep-sea sediments.
Sustainable solutions for the future of plastics
Thanks to recent pioneering developments, there are new solutions that can turn the tide. Innovative chemical recycling strategies, for example based on Sulzer’s devolatilization technology, are providing new recycling opportunities for traditional plastics. Sulzer recently announced its collaboration with Tide Ocean SA and the Eastern Switzerland University of Applied Sciences on a groundbreaking solution to recycle ocean-bound plastic waste. Sulzer Chemtech developed a method to turn recycled polyethylene terephthalate (PET) recovered from the ocean into high-quality foams that match the properties of virgin plastics. This is a key step towards forming premium raw materials that can be made into innovative circular products.
Moreover, new alternatives are offering more sustainable, yet highly performing, polymeric material without any compromise. The most widely adopted of such alternatives is PLA, a plastic obtained from sugars contained in crops and plants. It is renewable, biodegradable, compostable and recyclable — achieving circularity.
Increasingly used worldwide, PLA relies greatly on Sulzer Chemtech’s leading purification processes. Sulzer proprietary technology is included in almost all PLA production plants currently in operation, from small- to large-scale facilities, including the largest globally.
One ring (-opening polymerization) to rule them all
What makes PLA unique is that the bioplastic is made using a non-traditional chemical reaction known as ring-opening polymerization. This process allows us to deliver more robust materials, whose properties can be easily adjusted to suit different applications and uses. For example, it is possible to adapt the compostability of PLA, making it exceptionally resistant if used in durable products with long-term performance or easily degradable for disposable applications.
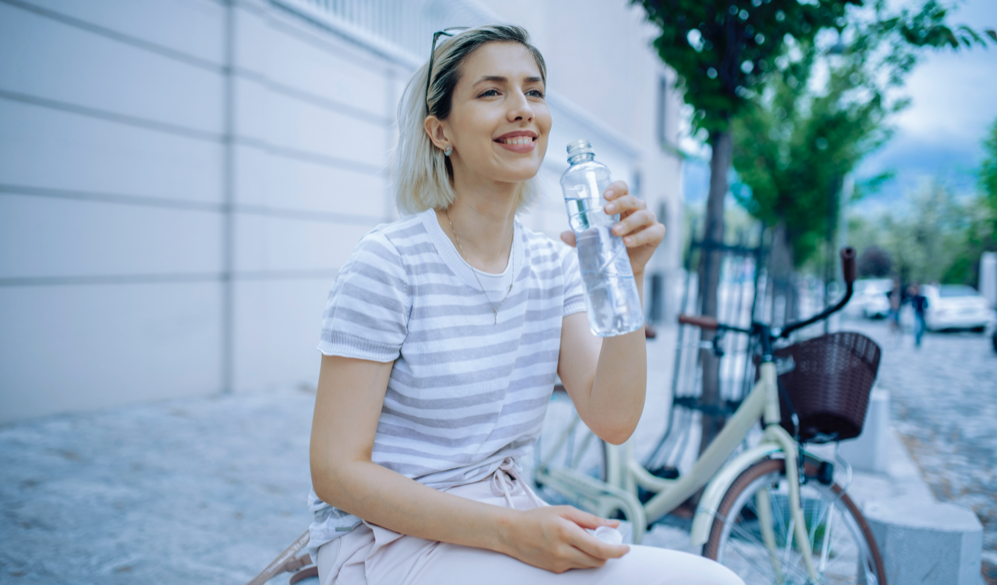
This allows us to revolutionize the plastic life cycle, solving the problem that has marred the plastics industry for decades. We give our customers full control over the technical properties of their bioplastics, so that they can be used long-term, easily recycled, or degradable in natural environments depending on their intended use. Businesses choosing our state-of-the-art technology can therefore produce a wide range of competitive and fully circular products that serve different industries and enhance their role in the marketplace.
Driving sustainability practices worldwide
When Corbion, a market leader in biotechnology, wanted to establish a new production facility for PLA, Sulzer Chemtech offered the right services and technologies in record time. In just over a year, we provided a complete, fully customized technology and project-management solution that enables the bioplastic manufacturer to deliver approximately 75’000 tons of sustainable bioplastics every year.
Thanks to our expertise and capabilities, the flexible production line can supply different types of PLA to support various applications, including packaging, consumer goods, 3D printing, fibers and automotive products. At the end of their service life, these products can be mechanically or chemically recycled, or even industrially composted to fertilize soil, making them truly sustainable, circular products.
Supporting continuous growth
NatureWorks, the world’s leading manufacturer of low-carbon PLA biomaterials, wanted to support the increasing global demand for bioplastics with a new production facility for PLA and its intermediates. Located in Nakhon Sawan Biocomplex, Thailand, this plant will have a capacity of approximately 75’000 tons of biopolymer annually.
To provide the key equipment for this facility, particularly for lactide and PLA production, NatureWorks selected its long-term partner, Sulzer Chemtech. A key reason was that our technology can purify lactide and its intermediates to reach extremely high levels, while the polymerization can support versatility in the types of plastics created. These elements will help NatureWorks maintain a competitive edge with a range of high-quality, sustainable products.
More information about our products and services at www.sulzer.com.