Steeled for the future
Sulzer engineers came up with a new repair method for steam turbines in geothermal power generation. The improved welding technique uses 12% chromium stainless steel. It gives rotors running in harsh conditions an extended life.
In 2017, Asia accounted for nearly two-thirds of the global increase in renewable energy generating capacity, according to a report by the International Renewable Energy Agency. One important energy source is the heat from the earth: renewable geothermal steam from underground. Four out of the top ten biggest geothermal power plants in the world are located in Asia (Indonesia and Philippines).
In power plants, steam turbines are used to convert steam energy into mechanical energy. This energy drives a generator that produces electrical energy. Power lines transport the energy to homes and businesses.
Innovation in the service business is part of our DNA. We improve our repair technologies and response time to optimize cost of ownership of our customers.
Daniel Bischofberger, Division President Rotating Equipment Services
Washed away by corrosion
Steam turbines operate under extreme temperatures and pressures. In addition, geothermal steam turbines work with steam that contains some very corrosive components. Because it is a natural process, they are variable and unpredictable. In practice, very substantial damage can occur over time due to corrosion and erosion, which can cause the areas exposed to the steam to be “washed away”.
The rotors used for these steam turbines employ a range of steels specially developed to retain their strength over a long operating life of 25 or even 30 years and to be corrosion-resistant.
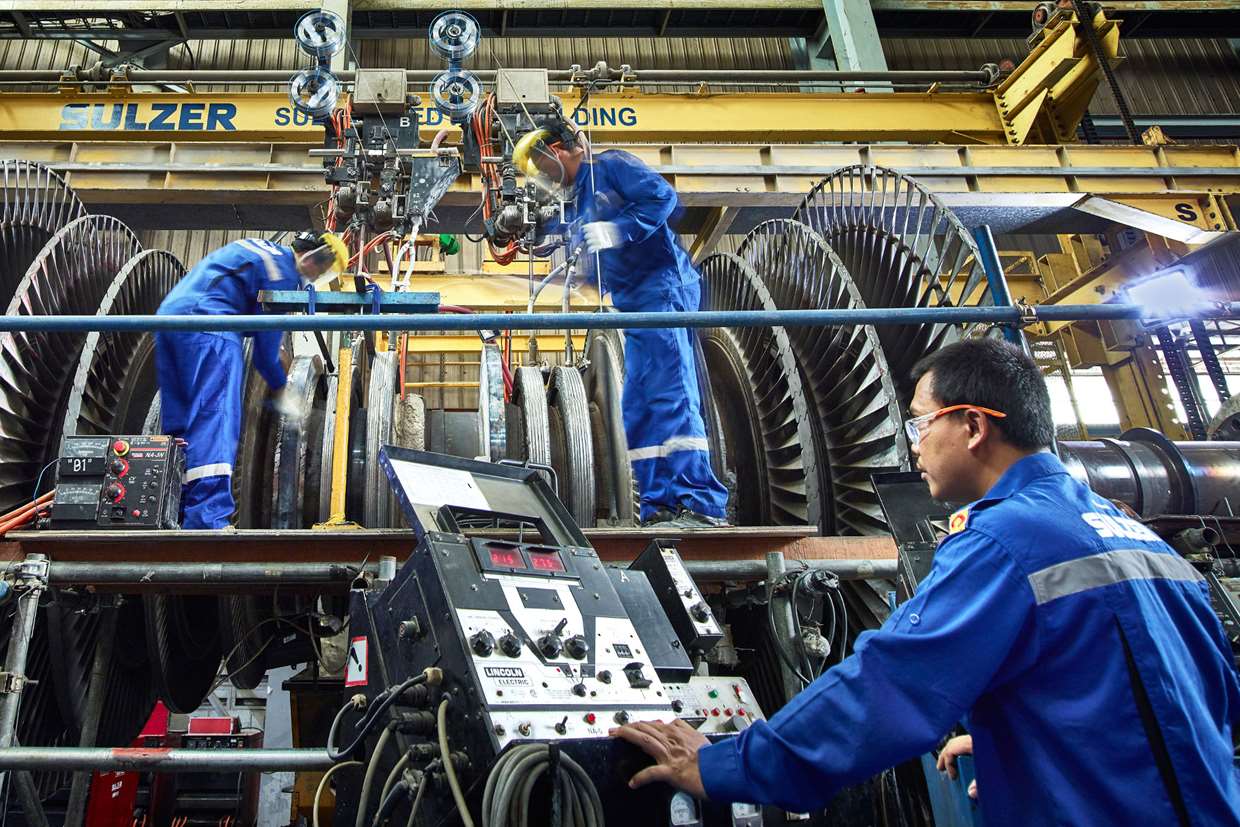
Welding instead of replacing
The fast repair of critical rotating components is one of the main activities of Sulzer’s Rotating Equipment Services division. Original equipment manufacturers often propose to customers the very costly option of purchasing new replacement rotors. Our Indonesian team saw a market opportunity to repair the rotors by welding.
In this process, an area of damaged material is removed and a large mass of weld material is used to replace it. The geometry is then recreated to finish the renovated rotor. This can be much quicker than ordering a replacement part because the long lead-time for new forgings can be avoided. Both the customer and Sulzer profit from the improved cost structure.
New ways to speed up delivery
Sulzer’s Rotating Equipment Services division is finding new ways to shorten the lead times and increase the quality of the parts it provides to customers.
Rapid casting, where we print the patterns from which we cast the parts, creates supply chain flexibility. It also enables manufacturing closer to the customer’s location. The division is gradually expanding its use of this technology within pumps services, region by region.
Collaborating for better resistance
The idea was born in 2013 at Sulzer Indonesia. A Philippine customer needed a rotor repair of a geothermal steam turbine that was showing cracks and stress corrosion.
The Sulzer team had some concerns about the weld material used at that time. A low-alloy weld wire for turbine rotor material typically has a high nickel content, which is likely to suffer corrosion cracking when exposed to a hostile environment. The Indonesian team consulted with Sulzer colleagues in the US and eventually came up with the 12% chromium steel (12Cr) weld wire option.
Extending rotor lifetime
The 12Cr weld has even greater corrosion resistance than similar alloys developed by the different rotor suppliers in the specific hostile environment where the geothermal steam is extracted from the rock. This means that in some cases, the 12Cr weld can actually give the renovated rotor an improved life over the original material.
The Sulzer Executive Committee recognized the innovative approach and exemplary collaboration of these two teams across a vast geographical distance by honoring them with a “Sulzer Innovation Award” in 2018.
More stories about our products and services at www.sulzer.com/stories.