– Focus – If you can’t eliminate your CO2 emissions, capture them!
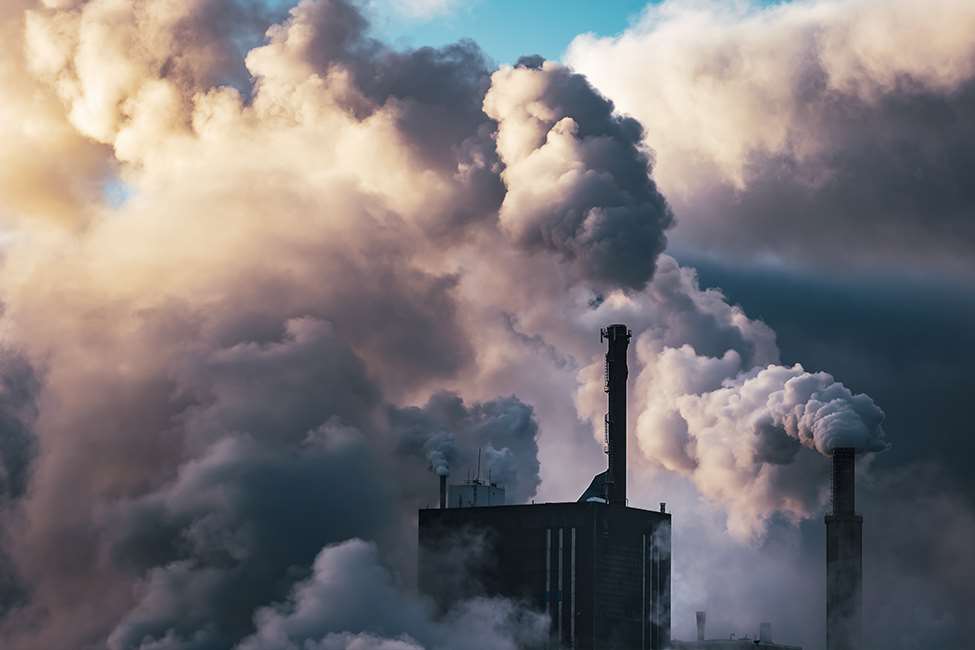

If you can’t eliminate your CO2 emissions, capture them!
Carbon capture, utilization and storage (CCUS) has a critically important role to play on the path to net zero. For those emissions that are impossible to completely eradicate through carbon reduction strategies, for example from industrial activities like hydrocarbon processing, Sulzer's CCUS solutions can help capture and transform the remaining emissions into valuable resources to be sold and used in a variety of sectors, thereby enabling circularity and the decarbonization of heavy industries.
Governments worldwide are setting ambitious targets aimed at reducing greenhouse gas (GHG) emissions to align with global net‑zero commitments. To achieve this, organizations are looking at ways to improve their environmental footprint while remaining competitive in a challenging marketplace.
While the priority of net‑zero strategies is to reduce carbon emissions to the greatest extent possible, we know that there are some sectors where the complete abatement of carbon emissions is nearly, if not entirely, impossible. Hydrocarbon processing, chemical manufacturing and power generation with fossil fuels – all of these industries will need to rely on capturing and safely storing those emissions that they cannot abate. Therefore, in the International Energy Agency’s Sustainable Development Scenario, in which global CO2 emissions from the energy sector fall to zero on a net basis by 2070, CCUS accounts for nearly 15% of the cumulative reduction in emissions1.
As a result, the growth of the carbon capture market in the period to 2070 is expected to follow an upward trend that is inversely proportional to the emission reduction requirements in the same period, creating significant opportunities for companies like Sulzer with the know-how to enable cost-efficient carbon capture, utilization and storage.
Emissions as resources
The most compelling and cost-effective way to deal with carbon emissions once captured is to utilize at least a part of them as a resource, in line with circularity principles. For example, captured CO2 can be used to produce sustainable aviation fuels – an energy application that is particularly hard to decarbonize. Carbon is also the key building block of chemicals and polymers and widely used in the healthcare sector and the food industry, e.g. for carbonated drinks. Moreover, it can support the production of carbon‑negative concrete by crystallizing the carbon and permanently storing it within concrete.
This creates additional incentives and opportunities for emissions-heavy businesses to capture their carbon – not only does society benefit, but there are also real financial gains to be realized by reusing the captured CO2 as a valuable resource. Hydrocarbon processing facilities can potentially become independent, closed-loop facilities, where the carbon generated by the main plant’s activities is then reintroduced into the system as feedstock to produce chemicals, materials or fuels. As a result, companies in this sector can address changing market needs and environmental regulations while generating new revenue streams and increasing their competitive advantages.
The critical component in carbon capture units is the separation technology that is used to separate the CO2 from the other flue gases produced during industrial processing. To deliver optimum performance in these separation columns, Sulzer has developed its proprietary MellapakCC™ structured packing, which was designed specifically for carbon capture applications. More precisely, this cost-effective technology increases efficiency by 20% when compared to conventional structured packing, while enabling the capture of the vast majority of carbon emissions.
For example, Sulzer’s technology is being used at a coal-fired power plant in Saskatchewan, Canada. The plant employs a highly advanced carbon capture system with internals and packing from Sulzer, which enables the direct capture of up to 90% of the CO2 emissions produced by the plant. By January 2022, 4’256’840 tons of CO2 had been captured and permanently sequestered since the carbon capture unit began operating in 20142.
Using and permanently storing captured carbon
As well as developing the technology to capture carbon emissions, Sulzer is driving innovation on ever more inventive methods of putting the carbon to good use while simultaneously providing safe storage solutions that prevent its release into the atmosphere. For example, Sulzer is working with Blue Planet on a ground-breaking mineralization process that permanently stores carbon emissions captured from heavy industries in aggregate form, which can then be used to produce carbon-negative concrete.
The technology combines captured CO2 with industrial waste to obtain synthetic limestone aggregate – one of the three key ingredients of concrete, along with cement and water. The mineralization process permanently locks up to 440 kg of CO2 into every tonne of aggregate produced. As a result, it is possible to completely offset the CO2 footprint of cement and produce carbon‑negative concrete. With concrete currently accounting for 7% of global emissions, this process represents a big step in the decarbonization of the construction industry.
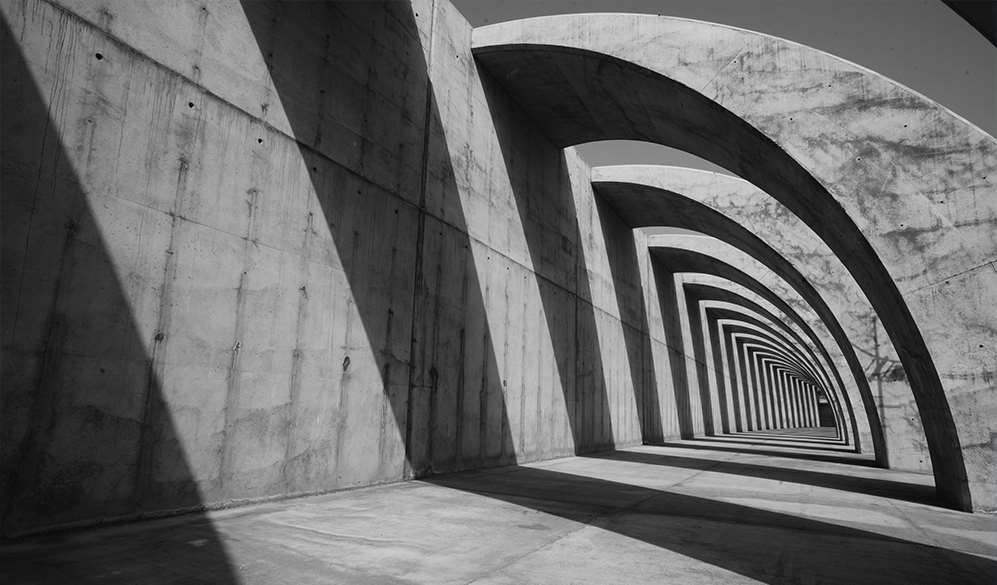
Another of Sulzer’s innovative methods of storing captured carbon is to convert the CO2 into high-pressure, supercritical form, which can be used to optimize oil recovery from depleted oil wells. Using highly specialized pumps from Sulzer, the CO2 is pumped into the well to extract oil with far greater efficiency than traditional methods using water. The pumped CO2 is then stored in the underground oil field, providing a perfect storage medium for the greenhouse gas. This groundbreaking circular process has the power to transform the oil and gas industry by reducing CO2 emissions while simultaneously maximizing recovery from existing oil fields – reducing the need for further oil exploration.
1) International Energy Agency: CCUS in clean energy transitions
2) Sask Power status update January 2022
More information about our products and services at www.sulzer.com.