Letter to the shareholders
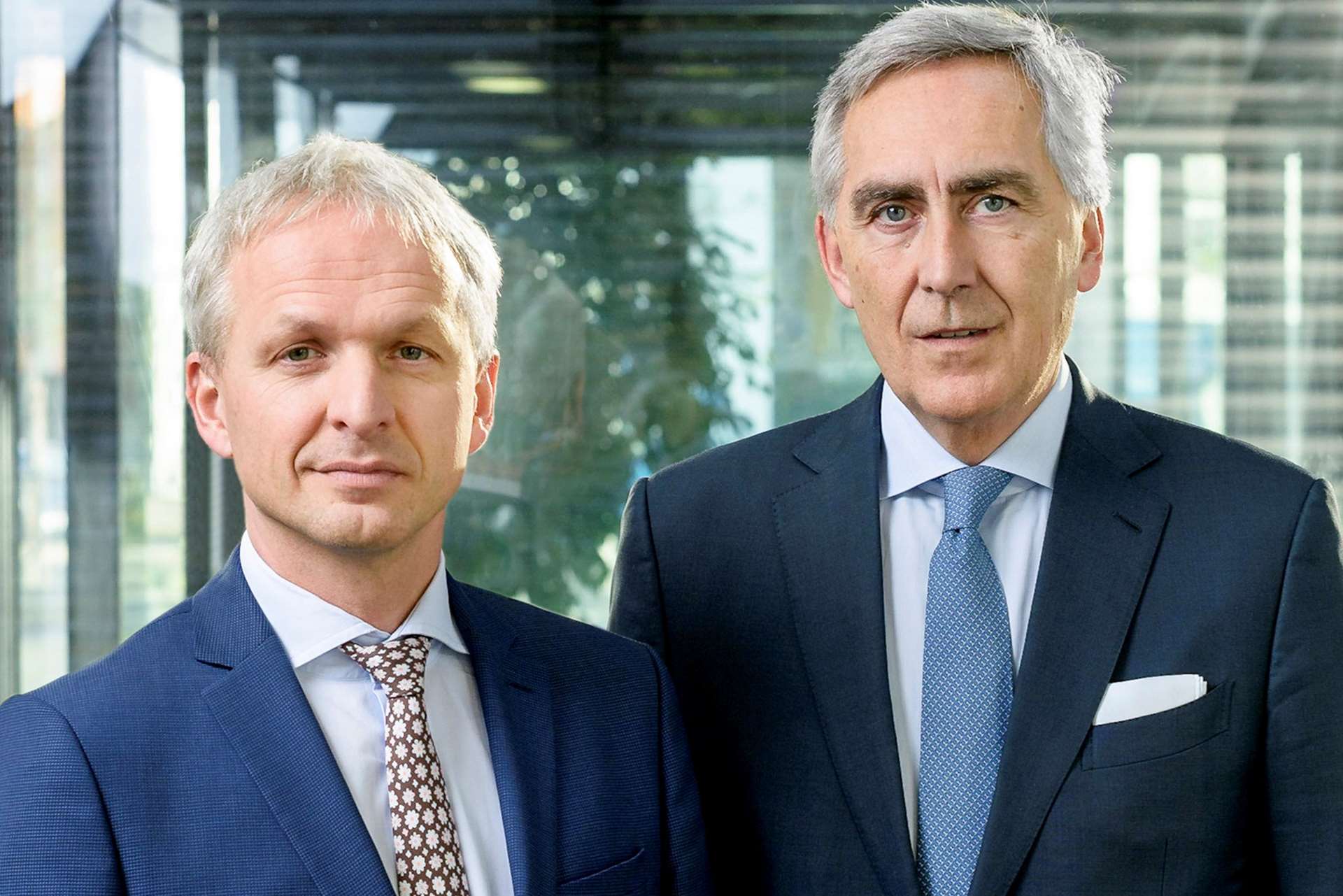
Dear Shareholder,
After a strong start to 2020, COVID-19 turned the world upside down. The World Health Organization declared the coronavirus outbreak a pandemic on March 11, and professional and private life has since changed dramatically. The health and safety of our employees remained our number one priority in this unprecedented situation, as we reconfigured the Sulzer network on the fly to continue to provide uninterrupted support to our customers. Sulzer’s broad regional presence, the balance between short and long-cycle businesses and our early actions to mitigate the impacts of COVID-19 were decisive factors that contributed to our resilience in the first half of 2020.
As an essential service provider, authorities around the world relied on Sulzer to continue to operate even during lockdowns. Our teams helped ensure that critical infrastructure, such as water and power utilities, transport systems and the healthcare sector, remained operational. We are proud of our people, who showed great dedication throughout these uncertain times and focused on serving our customers under the strictest safety precautions.
Strong order intake and a backlog reaching new heights
Overall order intake increased by 1.7% to CHF 1’840 million in the first six months of 2020. Our order backlog as of June 30 flirted with CHF 2 billion, a level not reached for many years and up 8.6% from the year before. Our aftermarket activities, which represent almost half of Sulzer, led the charge. With an increase in orders of 10.2%, Rotating Equipment Services continued its growth momentum across all product lines and regions, despite COVID-19-related access restrictions to customer sites.
Pumps Equipment reported growing orders of 6.0%, buoyed by its strong market position in the Middle East, China and Brazil and its negligible exposure to non-conventional oil (i.e. shale). We saw continued momentum in our Municipal and Waste Water activities, which grew by 2.5% organically. Orders in Chemicals went up strongly by 27.1%, while they decreased by 6.3% in Industry as COVID-19 softened industrial production around the world.
Chemtech order intake was 3.2% lower in the first half of 2020 compared with the same period of last year. While the Chemical market remained dynamic, decisions on larger projects drifted and we were particularly impacted by the lockdown in India, where we have a significant presence. This was counterbalanced by a Chinese market that went from strength to strength as the country reemerged from lockdowns.
After a strong start to the year, particularly in Beauty, our Applicator Systems division grinded to a halt in March as our customers were forced to suspend operations, leading to an order intake drop of 27.3% for the first half of 2020. Beauty and Dental felt the immediate impact of closures of cosmetics retailers and dental practices around the world. The Adhesives segment, which serves a wide range of markets such as the automotive, aviation and electronics industries, was impacted by temporary factory closures of customers. With the lifting of lockdowns, order intake and sales in all Applicator Systems segments started to recover late in the first half of 2020, a trend that is expected to continue and accelerate in the second half of the year.
Sulzer has again proven its resilience, which is based on its broad regional presence and a balance between early and late-cyclical business. We launched ambitious structural cost measures early in the pandemic to be well positioned for the market recovery.
Greg Poux-Guillaume, CEO
Lockdowns impacting sales and profitability
The lockdowns led to a standstill of public life in many countries, limited access to customer sites, travel restrictions and challenges in supply chain and sales channels. In this context, our diversified portfolio of applications and our global presence limited the revenue decrease to 3.9% in the first half of 2020.
Our teams took swift action to ensure the business continuity of our customers while implementing cost measures. This helped mitigate the impact of lower sales volumes, temporary factory closures and supply chain disruptions, resulting in an operational EBITA of CHF 120.2 million and a margin (opROSA) of 7.5%.
Adapting to changing market conditions
The pandemic has shown that it is crucial for an organization to be agile, in order to respond quickly to changing market conditions. As we announced in April, we aim to reduce our 2020 operational expenses by CHF 60 million to mitigate the impact of market disruptions triggered by COVID-19. Through cost-out measures, we have already reduced OPEX by CHF 21 million in the first half of the year.
In addition, we launched structural actions to make our Energy-related businesses leaner, in anticipation of adverse conditions in the oil and gas market which we expect to continue well into 2021. These actions will generate substantial savings of around CHF 70 million that will be fully realized over the next two years, with most of the uplift coming as early as 2021.
While we do this, we double down on investments that prepare us for the future – in additive manufacturing, data platforms, remote systems and digital production methods that will make us faster and more flexible.
Strategic investments in sustainable technology leaders
More than ever, we work to broaden our portfolio of bio-based technologies and circular applications. We strategically invest in technology companies that complement our offering and excel in innovative solutions for a greener future.
In June, Sulzer acquired 25% of technology company Tamturbo Plc, with a path to control. Tamturbo is a manufacturer of oil-free industrial air compressor systems that offers disruptive solutions. It enables cleaner and more energy-efficient compressed air production, complementing Sulzer’s market-leading low-pressure compressors for wastewater aeration. This positions us to serve a growing industrial automation market with increasing demand for oil-free compressed air, particularly for the food and beverage industry.
Sulzer also increased its investment in Worn Again, a company developing a unique polymer recycling process leveraging Sulzer technology to enable the recycling of textiles and polyester packaging. Sulzer and H&M, as strategic partners, control the company and are jointly betting on its future.
Through our leadership in process technology and energy-efficient solutions for various applications, Sulzer is forging ahead in developing sustainable solutions and fostering a circular economy.
Peter Löscher, Chairman of the Board of Directors
Outlook for 2020
The current business environment is characterized by high uncertainty, driven by COVID-19 and its economic fallout. Having initiated ambitious cost measures to mitigate the impacts of the pandemic, and based on our high order backlog, we are optimistic that we will continue to perform well. We expect the opEBITA margin (opROSA) to be at 8.5–9.0% for the full year 2020, and to return to around pre-pandemic levels for the full year 2021.
We want to thank our employees who, with their extraordinary commitment and dedication, have kept operations safe and running, living up to our deeply rooted culture of safety and service. We also express our sincere thanks to our loyal customers, our faithful partners and you, our shareholders, for your trust in this complicated period.
Stay healthy and safe.
Sincerely,
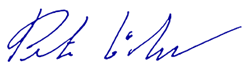
Peter Löscher
Chairman of the Board
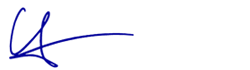
Greg Poux-Guillaume
CEO